Riksa uji drilling rig merupakan bagian dari riksa uji pesawat angkat dan angkut, karena drilling rig termasuk dalam kategori alat berat yang memiliki fungsi pengangkatan serta pemindahan komponen dalam proses pengeboran. Drilling rig, selain berfungsi untuk mengebor, juga memiliki sistem angkat yang digunakan untuk memindahkan pipa, peralatan pengeboran, dan material berat lainnya selama operasi berlangsung. Oleh karena itu, inspeksi terhadap sistem angkat pada drilling rig sangat mirip dengan pemeriksaan pada pesawat angkat dan angkut seperti crane, hoist, atau forklift.
Riksa uji ini meliputi pengecekan komponen mekanik, struktur rangka, serta sistem hidraulik yang digunakan untuk mengangkat dan menurunkan beban berat. Selain itu, pengujian dilakukan untuk memastikan bahwa alat tersebut mematuhi standar keselamatan yang berlaku, guna mencegah risiko kecelakaan kerja. Sama halnya dengan alat berat lainnya, kegagalan sistem angkat pada drilling rig dapat menyebabkan kecelakaan fatal, seperti runtuhnya struktur atau jatuhnya beban.
PJK3 adalah singkatan dari Perusahaan Jasa Keselamatan dan Kesehatan Kerja, yakni sebuah entitas yang diakui oleh pemerintah untuk memberikan layanan yang berkaitan dengan keselamatan dan kesehatan kerja (K3). Perusahaan ini bertanggung jawab dalam memastikan bahwa setiap aspek keselamatan dan kesehatan kerja di lingkungan industri telah memenuhi standar yang ditetapkan oleh peraturan perundang-undangan. PJK3 menyediakan layanan konsultasi, pelatihan, inspeksi, dan pengujian peralatan untuk memastikan kepatuhan terhadap syarat-syarat K3.
PJK3 Riksa Uji PT. Cipta Mas Jaya berkomitmen untuk memaksimalkan perlindungan infrastruktur melalui pemeriksaan dan pengujian drilling rig. Dalam proses ini, PT. Cipta Mas Jaya selalu menggunakan standar pengujian yang ditetapkan oleh pemerintah, memastikan setiap tahap inspeksi dilakukan sesuai dengan regulasi yang berlaku. Pengujian meliputi evaluasi struktur mekanik, pemeriksaan sistem hidraulik dan konektivitas komponen pada drilling rig, serta inspeksi perangkat pengangkatan dan pengamanan seperti pemutus sirkuit dan alat proteksi lainnya. Dengan menerapkan prosedur ketat dan teknologi terbaru, PT. Cipta Mas Jaya menjamin bahwa drilling rig berfungsi dengan optimal, melindungi operasional dari risiko kecelakaan, kerusakan peralatan, serta menjaga keamanan dan keselamatan di lingkungan kerja yang berisiko tinggi.
A. Definisi dan Prinsip Kerja Drilling Rig
Drilling rig adalah peralatan yang digunakan untuk membuat lubang di dalam tanah guna mencapai sumber daya yang ada di bawah permukaan bumi, seperti minyak, gas, dan air tanah. Perangkat ini terdiri dari beberapa komponen utama, seperti menara (derrick), bor, sistem pipa, dan mesin penggerak yang berfungsi untuk mengebor dengan kecepatan tinggi.
Prinsip kerja drilling rig melibatkan beberapa tahap yang saling berkaitan untuk memastikan pengeboran berlangsung secara efisien dan aman. Berikut adalah prinsip kerja umum dari drilling rig:
- Pengaturan Rig dan Persiapan Lokasi Langkah pertama dalam operasi drilling rig adalah pemasangan rig di lokasi pengeboran. Ini melibatkan pemasangan derrick, sistem hoisting, kelly drive, dan komponen utama lainnya. Selain itu, persiapan lokasi harus dilakukan untuk memastikan area pengeboran aman dan siap digunakan.
- Proses Pengeboran (Drilling)Drilling rig bekerja dengan memutar drill bit yang berada di ujung drill string. Drill string adalah rangkaian pipa yang panjang, yang dihubungkan dengan drill bit di bagian bawah dan sistem rotary table di bagian atas.
- Rotary table atau top drive memutar drill string sehingga drill bit dapat memotong formasi tanah atau batu di bawah permukaan.
- Ketika drill bit memutar, material yang terkikis oleh bit diangkut ke permukaan menggunakan drilling fluid (atau mud) yang dipompa melalui drill string dan keluar melalui bit.
- Drilling fluid juga berfungsi untuk mendinginkan drill bit, memberikan tekanan ke formasi, serta mencegah runtuhnya lubang bor.
- Pembuangan Cuttings Saat pengeboran berlangsung, potongan material yang terkerik oleh drill bit atau disebut cuttings, diangkut ke permukaan oleh drilling fluid. Cuttings kemudian dipisahkan dari mud menggunakan shale shaker dan peralatan lain seperti desilter dan desander. Cairan pengeboran yang sudah bersih dipompa kembali ke dalam lubang bor untuk melanjutkan proses pengeboran.
- Menambah Pipa Bor (Making a Connection) Seiring bertambahnya kedalaman pengeboran, drill string harus diperpanjang dengan menambah pipa bor baru. Proses ini dikenal sebagai making a connection, di mana rig akan menghentikan sementara pengeboran untuk menambahkan segmen pipa baru ke drill string.
- Pengangkatan (Tripping) Setelah pengeboran mencapai kedalaman yang diinginkan atau ketika drill bit perlu diganti, drill string diangkat dari lubang bor melalui proses yang disebut tripping. Proses ini melibatkan pengangkatan secara bertahap dan pemisahan pipa bor satu per satu hingga seluruh drill string berhasil dikeluarkan dari lubang bor.
- Casing dan Cementing Setelah pengeboran selesai, untuk memastikan lubang bor tetap stabil dan mencegah runtuhnya dinding lubang, dipasang casing (pipa baja) di sepanjang dinding lubang bor. Casing ini kemudian disemen untuk memberikan perlindungan dan mencegah kebocoran.
B. Bahaya dari Drilling Rig yang Tidak Diuji
Drilling rig merupakan peralatan yang kompleks dan beroperasi di lingkungan yang berisiko tinggi. Jika tidak diuji atau diperiksa secara berkala, berbagai bahaya dapat muncul, yang dapat membahayakan keselamatan operator, lingkungan sekitar, serta operasi pengeboran itu sendiri. Berikut beberapa bahaya yang signifikan jika drilling rig tidak diuji:
- Keruntuhan Struktur Rig Drilling rig memiliki komponen-komponen utama seperti derrick dan sistem hoisting yang harus mampu menopang beban berat. Tanpa pengujian yang rutin, ada risiko kegagalan struktural yang bisa menyebabkan runtuhnya rig. Hal ini dapat menyebabkan cedera serius atau bahkan kematian bagi para pekerja yang berada di area pengeboran.
- Kebocoran Sistem Hidrolik Drilling rig banyak bergantung pada sistem hidrolik untuk menggerakkan komponen-komponennya, seperti top drive dan draw works. Jika tidak diuji, kebocoran hidrolik dapat terjadi, yang dapat memicu kegagalan operasional dan potensi kecelakaan. Kebocoran ini juga bisa menyebabkan kontaminasi lingkungan, terutama jika minyak hidrolik tumpah ke tanah atau air di sekitar lokasi pengeboran.
- Ledakan dan Kebakaran Sistem pengeboran berurusan dengan fluida dan gas yang mudah terbakar. Jika blowout preventer (BOP) atau sistem keselamatan lainnya tidak diuji secara teratur, bisa terjadi kegagalan dalam mengontrol tekanan bawah tanah, yang bisa menyebabkan ledakan gas atau blowout. Hal ini sangat berbahaya karena berpotensi memicu kebakaran besar di area pengeboran.
- Kegagalan Peralatan Pengangkatan Winch dan sling yang digunakan untuk mengangkat pipa bor atau beban berat lainnya harus diuji secara berkala. Jika tidak, tali sling bisa aus atau putus, yang menyebabkan jatuhnya beban dari ketinggian. Kecelakaan seperti ini bisa berakibat fatal, menghancurkan peralatan lain, serta menyebabkan kerugian finansial yang besar.
- Kontaminasi Fluida Pengeboran Fluida pengeboran atau drilling mud digunakan untuk mendinginkan dan melumasi drill bit, serta mengangkut potongan bor ke permukaan. Jika sistem penanganan fluida tidak diuji dan rusak, hal ini dapat menyebabkan kegagalan dalam pengendalian tekanan atau kebocoran lumpur, yang dapat mencemari lingkungan dan menimbulkan risiko kesehatan bagi pekerja.
- Gagalnya Sistem Pengaman dan Sensor Drilling rig dilengkapi dengan berbagai sensor dan sistem otomatis untuk memantau tekanan, suhu, dan kondisi operasional lainnya. Jika sensor ini tidak berfungsi karena kurangnya pengujian, operator tidak dapat mendeteksi masalah lebih awal, yang dapat menyebabkan kegagalan serius seperti blowout atau ledakan. Sistem penghenti darurat yang tidak bekerja dengan baik juga bisa menambah tingkat risiko ketika terjadi situasi darurat.
- Risiko Kecelakaan akibat Kondisi Lingkungan Drilling rig sering dioperasikan di lokasi-lokasi yang ekstrem, seperti laut lepas, gurun, atau daerah dingin. Perubahan suhu dan cuaca dapat mempercepat keausan komponen rig. Tanpa pengujian berkala untuk memastikan keandalan rig di bawah kondisi lingkungan yang berubah-ubah, risiko kecelakaan meningkat, termasuk risiko tergelincir atau jatuhnya struktur akibat cuaca buruk.
C. Komponen yang Diperiksa dalam Riksa Uji Drilling Rig
Riksa uji drilling rig melibatkan pemeriksaan mendalam pada berbagai komponen penting yang berperan langsung dalam operasional pengeboran. Setiap bagian dari drilling rig harus berfungsi dengan baik untuk menjamin keselamatan dan efisiensi operasional. Beberapa komponen utama yang diperiksa dalam proses riksa uji drilling rig meliputi:
- Derrick dan Substruktur Derrick adalah menara pengeboran yang digunakan untuk menopang dan mengangkat pipa bor serta komponen lainnya. Pemeriksaan pada derrick dan substruktur meliputi pengecekan kondisi fisik, tanda-tanda keausan, korosi, dan keretakan. Selain itu, kekuatan struktural diperiksa untuk memastikan bahwa derrick mampu menahan beban yang dioperasikan, terutama saat mengangkat pipa dan alat pengeboran lainnya.
- Sistem Hoisting dan Draw Works Sistem hoisting berperan dalam mengangkat dan menurunkan pipa bor ke dalam lubang pengeboran. Komponen penting seperti draw works, crown block, dan traveling block harus diperiksa secara menyeluruh. Inspeksi ini bertujuan untuk mengecek kelayakan drum, rem, dan gear, memastikan tidak ada keausan yang signifikan yang dapat memicu kegagalan operasional atau risiko kecelakaan.
- Blowout Preventer (BOP) BOP adalah salah satu komponen paling kritis dalam drilling rig, yang berfungsi untuk mencegah terjadinya blowout atau ledakan yang disebabkan oleh tekanan bawah tanah yang tak terkendali. Riksa uji BOP melibatkan pengujian mekanisme penutupan, pengecekan terhadap ram dan annular preventer, serta memastikan bahwa seluruh sistem pengontrol tekanan bekerja dengan baik. Kegagalan pada BOP bisa mengakibatkan bencana besar, termasuk ledakan gas dan minyak yang tidak terkendali.
- Sistem Hidrolik dan Pneumatik Drilling rig bergantung pada sistem hidrolik dan pneumatik untuk berbagai fungsi, mulai dari pengangkatan hingga kontrol pergerakan komponen rig. Dalam riksa uji, kebocoran pada pipa hidrolik, tekanan hidrolik yang tidak stabil, serta performa pompa hidrolik dan pneumatik diperiksa secara menyeluruh. Pengujian juga dilakukan untuk memastikan bahwa tekanan kerja sesuai dengan spesifikasi yang diperlukan.
- Top Drive dan Rotary Table Top drive dan rotary table adalah komponen penting yang menggerakkan pipa bor. Keduanya berfungsi untuk memutar pipa bor dalam proses pengeboran. Riksa uji pada top drive dan rotary table melibatkan pengecekan pada gearbox, sistem penggerak, dan pelumas. Hal ini dilakukan untuk mengidentifikasi adanya keausan, keretakan, atau potensi kegagalan yang dapat memengaruhi proses pengeboran.
- Winch dan Tali Sling Tali sling dan winch digunakan dalam pengangkatan berbagai peralatan pengeboran serta pipa. Riksa uji pada winch dan tali sling berfokus pada pengecekan kekuatan tali, keausan, kerusakan pada permukaan tali, serta sistem rem pada winch. Tali yang sudah rusak atau aus dapat meningkatkan risiko kecelakaan karena potensi jatuhnya beban yang sedang diangkat.
- Sistem Kelistrikan dan Elektronik Sistem kelistrikan berfungsi untuk mengoperasikan berbagai peralatan pengeboran, termasuk kontrol otomatis dan sistem keselamatan. Riksa uji melibatkan pemeriksaan terhadap switchgear, panel kontrol, kabel, dan sensor elektronik untuk memastikan tidak ada gangguan atau potensi bahaya listrik. Sistem sensor juga diuji untuk memastikan bahwa mereka dapat mendeteksi potensi masalah operasional dan memberikan peringatan dini.
- Pipa dan Drill String Drill string adalah rangkaian pipa bor yang digunakan untuk pengeboran sumur. Riksa uji pada pipa bor melibatkan pengecekan pada sambungan pipa (tool joint), memastikan tidak ada retak, korosi, atau deformasi yang bisa menyebabkan kegagalan selama operasi pengeboran. Sambungan yang buruk dapat menyebabkan patahnya pipa di dalam sumur, yang akan mempersulit operasi pengeboran dan menyebabkan keterlambatan.
- Sistem Pengangkatan dan Transportasi Drilling rig seringkali diangkut dari satu lokasi ke lokasi lain, terutama untuk rig darat. Oleh karena itu, sistem pengangkatan dan transportasi, seperti track dan skid, juga diperiksa untuk memastikan bahwa seluruh sistem dapat bekerja dengan aman dan efisien saat rig dipindahkan. Sistem ini diperiksa dari segi kekuatan mekanis, kondisi roda atau trek, serta keausan pada komponen-komponen penggeraknya.
- Sistem Keselamatan dan Penghenti Darurat Sistem keselamatan seperti sensor, alarm, dan emergency shut down (ESD) memainkan peran penting dalam mencegah kecelakaan besar. Riksa uji mencakup pemeriksaan fungsionalitas sensor tekanan, suhu, dan detektor gas berbahaya. Selain itu, tombol darurat diperiksa untuk memastikan bahwa dalam situasi darurat, sistem dapat menghentikan operasi secara instan.
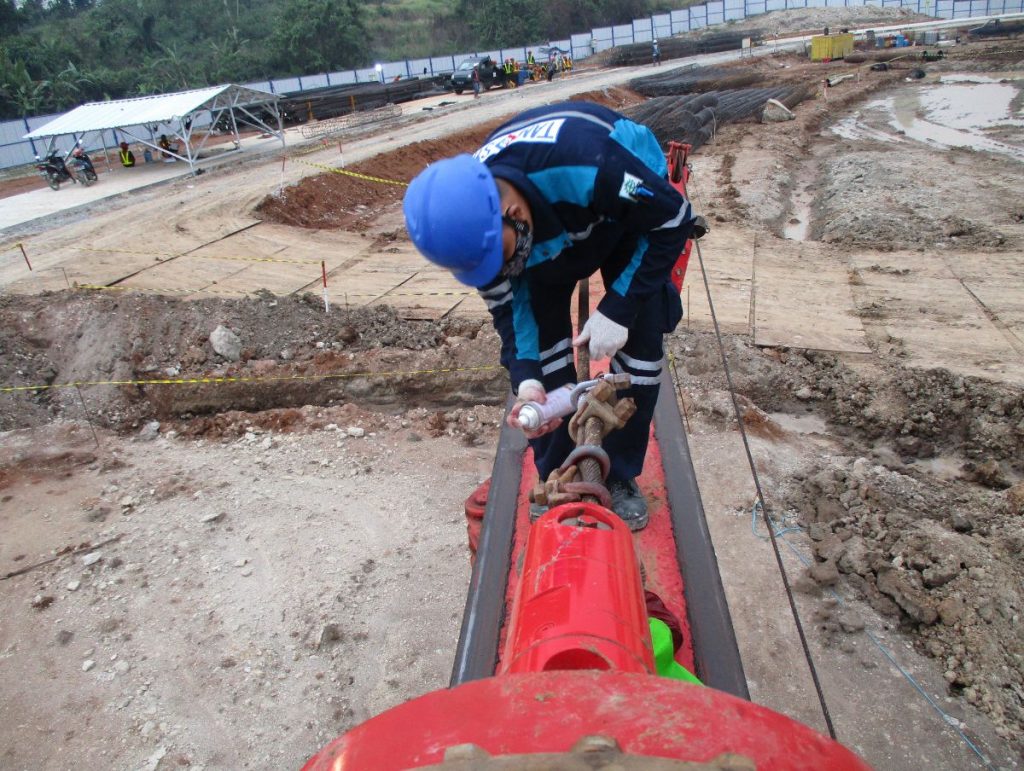
D. Keuntungan Melakukan Riksa Uji Drilling Rig
Melakukan riksa uji secara berkala pada drilling rig memberikan banyak keuntungan baik dari segi keselamatan, efisiensi, maupun operasional. Beberapa keuntungan utama dari riksa uji drilling rig meliputi:
- Meningkatkan Keselamatan Kerja Drilling rig merupakan salah satu peralatan berat yang beroperasi dalam lingkungan berisiko tinggi, terutama dalam proses pengeboran minyak dan gas. Dengan melakukan riksa uji, potensi bahaya yang disebabkan oleh kerusakan alat dapat diidentifikasi lebih awal. Komponen penting seperti winch, tali sling, sistem kontrol, dan sistem keselamatan diperiksa secara teliti untuk memastikan bahwa tidak ada masalah yang bisa menyebabkan kecelakaan kerja. Keselamatan pekerja menjadi prioritas utama dalam industri ini, dan riksa uji berperan penting dalam mengurangi kemungkinan terjadinya kecelakaan serius seperti ledakan atau kebocoran minyak dan gas.
- Mencegah Downtime dan Mengurangi Biaya Perbaikan Kegagalan operasional drilling rig akibat kerusakan komponen dapat mengakibatkan downtime yang signifikan. Waktu henti ini tidak hanya menyebabkan keterlambatan dalam proyek pengeboran, tetapi juga bisa sangat merugikan secara finansial. Dengan melakukan riksa uji secara teratur, potensi masalah dapat diidentifikasi dan diperbaiki sebelum kerusakan besar terjadi. Ini membantu mengurangi biaya perbaikan yang mendadak, karena perawatan pencegahan biasanya lebih murah dibandingkan dengan perbaikan darurat setelah kegagalan besar. Keandalan peralatan juga terjaga, sehingga operasional dapat berjalan sesuai rencana tanpa hambatan yang tidak terduga.
- Mematuhi Standar dan Peraturan Keselamatan Industri pengeboran minyak dan gas memiliki standar keselamatan yang ketat, yang mengharuskan operator untuk memastikan bahwa peralatan mereka, termasuk drilling rig, diuji secara berkala. Melalui riksa uji, operator memastikan bahwa mereka mematuhi peraturan nasional dan internasional yang mengatur penggunaan peralatan pengeboran. Kegagalan untuk memenuhi standar ini bisa berujung pada sanksi hukum, denda, atau penghentian operasi. Dengan melakukan riksa uji, perusahaan dapat menjaga reputasi mereka dan menghindari konsekuensi hukum yang merugikan.
- Memperpanjang Umur Peralatan Peralatan pengeboran, termasuk drilling rig, mengalami keausan dari waktu ke waktu akibat penggunaan yang berat. Riksa uji secara rutin membantu dalam mengidentifikasi bagian-bagian yang mengalami keausan sebelum menyebabkan kerusakan serius. Melalui perawatan yang tepat waktu, komponen yang aus dapat diganti atau diperbaiki, yang pada akhirnya akan memperpanjang umur drilling rig secara keseluruhan. Investasi dalam riksa uji rutin dapat menghasilkan penghematan jangka panjang karena mengurangi frekuensi penggantian komponen besar dan memperpanjang siklus hidup alat tersebut.
- Meningkatkan Efisiensi Operasional Drilling rig yang beroperasi dengan kondisi optimal berkontribusi langsung pada efisiensi operasional. Ketika semua komponen berfungsi dengan baik, waktu operasional dapat dioptimalkan, sehingga proyek pengeboran dapat diselesaikan lebih cepat dan sesuai jadwal. Riksa uji membantu memastikan bahwa peralatan berfungsi pada kapasitas maksimumnya tanpa adanya hambatan teknis. Ini juga berpengaruh pada penghematan bahan bakar dan energi, karena rig yang terpelihara dengan baik biasanya bekerja lebih efisien.
- Meningkatkan Kepercayaan Klien dan Stakeholder Bagi perusahaan yang menggunakan drilling rig, melakukan riksa uji secara teratur menunjukkan komitmen terhadap keselamatan dan kualitas operasional. Ini tidak hanya penting bagi para pekerja dan operator, tetapi juga bagi klien dan stakeholder lainnya. Perusahaan yang mampu menjaga peralatan mereka dalam kondisi prima akan mendapatkan kepercayaan lebih dari klien, karena hal tersebut menjamin bahwa proyek dapat diselesaikan dengan aman, tepat waktu, dan sesuai anggaran yang direncanakan.
Secara keseluruhan, riksa uji drilling rig tidak hanya menjamin keselamatan kerja dan kepatuhan terhadap peraturan, tetapi juga mendukung efisiensi operasional, penghematan biaya, dan kelangsungan hidup proyek pengeboran yang berkelanjutan.
E. Peran PJK3 dalam Riksa Uji Drilling Rig
Perusahaan Jasa Keselamatan dan Kesehatan Kerja (PJK3) memainkan peran vital dalam proses riksa uji drilling rig. Sebagai pihak yang memiliki otoritas dan keahlian dalam melakukan inspeksi dan pengujian peralatan berat, PJK3 bertanggung jawab memastikan bahwa semua aspek keselamatan terpenuhi sesuai dengan standar yang berlaku. Berikut adalah peran utama PJK3 dalam riksa uji drilling rig:
- Melakukan Inspeksi Teknis dan Keselamatan PJK3 bertugas melakukan pemeriksaan menyeluruh terhadap drilling rig, termasuk komponen-komponen penting seperti sistem hidrolik, winch, tali sling, serta sistem kontrol dan keselamatan. Inspeksi ini dilakukan untuk mendeteksi potensi kerusakan atau malfungsi yang bisa memengaruhi performa alat. Dengan tim yang berpengalaman dan bersertifikat, PJK3 memastikan bahwa setiap komponen berfungsi dengan optimal dan memenuhi standar keselamatan yang ditetapkan oleh regulasi industri.
- Mengidentifikasi Risiko dan Memberikan Rekomendasi Selain melakukan inspeksi teknis, PJK3 juga mengidentifikasi risiko-risiko yang mungkin terjadi selama operasional drilling rig. Mereka memberikan rekomendasi tentang perbaikan atau tindakan preventif yang perlu dilakukan untuk meminimalisir potensi bahaya. Ini termasuk memberikan saran terkait perawatan rutin, penggantian komponen yang sudah aus, atau perbaikan pada bagian-bagian yang terdeteksi memiliki kerusakan.
- Mengeluarkan Sertifikat Kelaikan Operasional Setelah riksa uji selesai dilakukan, PJK3 akan memberikan sertifikat kelaikan operasional bagi drilling rig yang telah memenuhi standar keselamatan dan operasional. Sertifikat ini menjadi bukti bahwa alat tersebut aman untuk digunakan dalam operasi pengeboran. Tanpa sertifikasi ini, penggunaan drilling rig dianggap tidak aman dan bisa mengakibatkan sanksi dari pihak berwenang atau regulasi.
- Memastikan Kepatuhan terhadap Peraturan dan Standar Keselamatan PJK3 memastikan bahwa drilling rig yang diuji telah mematuhi semua regulasi keselamatan yang berlaku, baik pada tingkat nasional maupun internasional. Mereka memiliki pengetahuan mendalam tentang standar yang diterapkan dalam industri pengeboran, seperti standar dari OSHA (Occupational Safety and Health Administration) dan SNI (Standar Nasional Indonesia). Dengan demikian, peran PJK3 tidak hanya sebatas pengujian teknis, tetapi juga memastikan kepatuhan terhadap peraturan keselamatan.
- Memberikan Pelatihan dan Edukasi PJK3 juga berperan dalam memberikan pelatihan dan edukasi kepada operator drilling rig dan tim teknis terkait prosedur keselamatan dan perawatan alat. Mereka memberikan panduan tentang cara mengoperasikan drilling rig dengan aman serta cara melakukan pemeriksaan harian untuk mendeteksi potensi masalah. Dengan pelatihan ini, tim di lapangan dapat lebih siap menghadapi situasi darurat dan memahami pentingnya perawatan preventif.
- Mengurangi Risiko Kecelakaan Kerja Dengan adanya PJK3 yang terlibat dalam riksa uji, risiko kecelakaan kerja yang melibatkan drilling rig dapat diminimalisir. Mereka bertindak sebagai pihak independen yang menilai secara objektif kondisi peralatan dan potensi bahaya. Hal ini membantu perusahaan mengidentifikasi dan mengatasi masalah sebelum terjadi kegagalan operasional atau kecelakaan fatal.
Secara keseluruhan, peran PJK3 dalam riksa uji drilling rig sangat penting dalam menjaga keselamatan operasional, mencegah terjadinya kecelakaan kerja, serta memastikan bahwa semua peralatan beroperasi sesuai standar yang telah ditetapkan. Mereka tidak hanya memverifikasi kelaikan teknis peralatan, tetapi juga mendukung terciptanya lingkungan kerja yang aman dan produktif.
F. Regulasi yang Mengatur Riksa Uji Drilling Rig
Dalam pelaksanaan riksa uji drilling rig, terdapat beberapa regulasi dan standar yang harus dipatuhi. Beberapa di antaranya adalah:
- Peraturan Menteri Tenaga Kerja tentang Alat Berat: Peraturan ini mengatur tentang keselamatan penggunaan alat berat termasuk drilling rig, serta persyaratan inspeksi berkala.
- Standar Internasional: Drilling rig juga harus memenuhi standar keselamatan internasional seperti yang dikeluarkan oleh organisasi seperti ISO (International Organization for Standardization) dan OSHA (Occupational Safety and Health Administration).
G. Kesimpulan
Riksa uji drilling rig adalah langkah penting untuk memastikan keselamatan dan efisiensi operasional alat berat yang digunakan dalam industri pengeboran. Tanpa pengujian rutin, drilling rig berisiko mengalami kerusakan atau kegagalan yang dapat membahayakan nyawa pekerja serta merugikan perusahaan. Pemeriksaan menyeluruh terhadap komponen-komponen utama seperti sistem hidrolik, winch, tali sling, serta sistem kontrol dan keselamatan adalah kunci untuk memastikan rig berfungsi optimal dan aman digunakan.
Dengan melakukan riksa uji secara berkala, perusahaan dapat meminimalisir risiko kecelakaan kerja, meningkatkan efisiensi operasional, dan memastikan kepatuhan terhadap regulasi keselamatan yang berlaku. Peran PJK3 sangat esensial dalam proses ini, mulai dari melakukan inspeksi teknis hingga memberikan rekomendasi perbaikan dan sertifikasi kelaikan operasional. Dengan demikian, riksa uji drilling rig tidak hanya mendukung keselamatan pekerja tetapi juga menjaga performa alat dan keberlanjutan operasi industri pengeboran.
Artikel Terkait:
Riksa Uji Crawler Crane
Riksa uji crawler crane adalah proses inspeksi mendalam yang dilakukan untuk memastikan bahwa alat berat ini memenuhi standar keselamatan dan...
Riksa Uji Instalasi Listrik: Kunci untuk Mencegah Bahaya dan Menjamin Keamanan!
Riksa uji instalasi listrik adalah inspeksi teknis dan pengujian menyeluruh yang bertujuan untuk memastikan bahwa instalasi listrik sesuai dengan standar...
Riksa Uji Eskalator
Riksa uji eskalator adalah proses pemeriksaan dan pengujian yang dilakukan secara berkala untuk memastikan bahwa eskalator beroperasi dengan aman dan...
Riksa Uji Deaerator
Riksa uji deaerator adalah proses penting dalam pemeliharaan peralatan pembangkit tenaga uap yang meliputi pemeriksaan fisik dan fungsional komponen utama,...
Riksa Uji Jib Crane
Riksa uji jib crane adalah proses pemeriksaan teknis yang dilakukan untuk memastikan bahwa jib crane berfungsi dengan aman dan efisien...
Artikel Yang Diperbarui:
Pengujian Non Destruktif (NDT)
Pengujian Non Destruktif atau Non-Destructive Testing (NDT) adalah teknik pemeriksaan material yang memungkinkan evaluasi tanpa harus merusak atau mengubah bentuk...
Ultrasonic Testing (UT) – Pengujian Ultrasonik
Ultrasonic Testing adalah metode Non-Destructive Testing (NDT) yang menggunakan gelombang ultrasonik frekuensi tinggi untuk mendeteksi cacat internal, mengukur ketebalan material,...
Keuntungan Menggunakan Forklift Listrik Mitsubishi di Gudang
Temukan berbagai keuntungan menggunakan forklift listrik Mitsubishi di gudang, termasuk efisiensi energi, pengurangan emisi, dan biaya operasional yang lebih rendah....
Riksa Uji Instalasi Listrik: Kunci untuk Mencegah Bahaya dan Menjamin Keamanan!
Riksa uji instalasi listrik adalah inspeksi teknis dan pengujian menyeluruh yang bertujuan untuk memastikan bahwa instalasi listrik sesuai dengan standar...
Riksa Uji Hydrant
Riksa uji hydrant adalah proses pemeriksaan, pengujian, dan pemeliharaan yang dilakukan secara berkala untuk memastikan bahwa sistem hydrant berfungsi dengan...